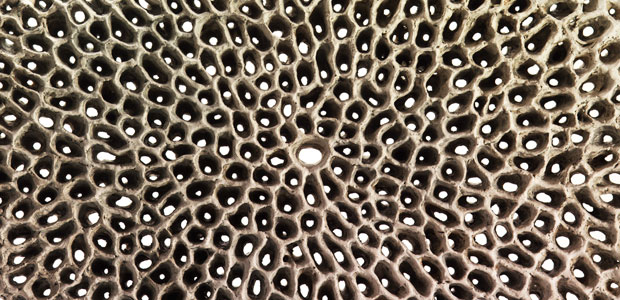
Paper clay is any clay body to which processed cellulose fiber has been added. Adding paper pulp and other fibers to your clay body can make things you never thought possible with clay totally doable. This is why many sculptors make paper clay sculpture. Paper clay helps reduce shrinkage in the drying stage and strengthen joints, allowing wet and dry pieces to be joined. Think your mug has dried too much to attach a handle? With paper clay, it’s not an issue.
In today’s post, an excerpt from Additions to Clay Bodies, Kathleen Standen explains the ins and outs of working with paper clay. She also shares how Barbro Aberg makes her paper clay sculpture.
Strengthening Your Work with Paper Clay
The most commonly used fiber is cellulose, made from paper pulp. Ceramicists generally have a favorite paper they use, such as newspaper, egg cartons or toilet paper. The proportion of clay slip to paper pulp varies, but a typical sample would be 4:1. The clay slip and paper pulp are mixed thoroughly together, with the best results achieved using a blender or electric mixer. The blended mixture is then laid out on plaster batts to dry a little so it can be wedged into balls of clay. The proportions can vary from 5% to 25%; carrying out your own investigations is the best way to find out what suits your work. This post from the archives further explains how to make paper clay.
Making your own paper clay is economical and versatile, as any clay body can be used. There are some issues to be aware of:
The shelf life of homemade paper clay is about two weeks, so it needs to be used up quickly; if kept for longer, the organic cellulose starts to break down and decay (Kathleen discusses the health issues around this in Chapter 3 of Additions to Clay Bodies).
When paper clay decays, the tubular structure of the cellulose fibers breaks down and the paper clay loses the properties associated with it; toilet paper is more prone to rapid decay because of a corn-starch coating on the cellulose fibers.
The usability of paper clay can be extended by adding a small amount of Milton sterilizing liquid or disinfectant (but not bleach) to the wet mixture before drying.
Alternatively, rolling out unused paper clay into thin sheets and allowing them to dry completely preserves the tubular structure of the fibers. They can be stored, and later softened up by laying them out on a damp cloth. See this post for paper
clay tips to extend the shelf life of paper clay!
Paper Clay Alternative: Cotton Fiber and Clay
An excellent alternative to paper pulp is the addition of cotton fibers. This can be purchased in sheets as cotton linter. Preparation of the materials is the same as for paper but cotton fibers don’t break down as easily as paper, so it can be stored in its wet form for longer. If you don’t want all this hassle, then the pottery suppliers listed at the back of the Additions to Clay Bodies will sell you a ready-made paper clay with an unlimited shelf life (as long as
it is wrapped up well).
Barbro Aberg’s Paper Clay Sculpture
Barbro Aberg’s large-scale paper clay sculptures are not easily categorized. As a Swede living in Denmark, combined with a five-year stint in the US, she has developed her own distinctive style. She exhibits her ceramics in galleries and events throughout Europe and the US.
She was introduced to additions early on: to perlite by US artist Bob Shay and paper clay by Rosette Gault. Testing of several different mixtures followed, until she found the correct formulae to suit her way of working. “During the years, I have developed several specific clay bodies: one for large, solid work, one for small pieces and one for open structures,” Aberg says. “They give me a range of possibilities for working freely with my sculptures.”
Most of her paper clay sculpture is modeled by hand, a slow process that allows Aberg to change the form as she constructs it. Larger pieces can take 6-7 weeks to finish. “I allow myself to reflect, alter and change, follow the impulses that emerge, and give room for a dialogue with each sculpture.” The work is fired to 1135-1140˚C (2075-2084˚F) in an electric kiln, often more than twice, or until the right surface is achieved. Terra sigillata is sometimes applied to the surface.