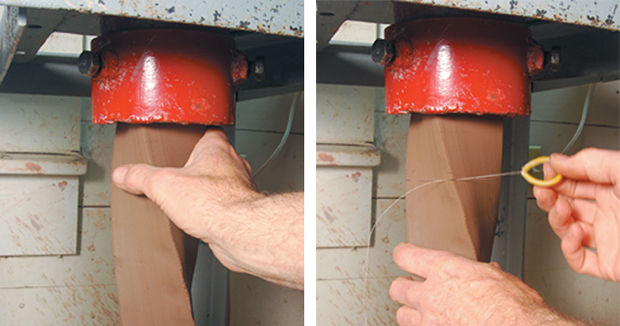
Extruders are great tools for the clay studio and it is super fun to use them to make extruded pottery or sculpture. They can be mounted to the wall or handheld, which is one of the reasons why they are a versatile tool.
To help you make sure you get the most out of your clay extruder, we’ve enlisted Daryl Baird, author of The Extruder Book, to come up with 20 extruder tips to improve your extruder experience! –Jennifer Poellot Harnetty, editor
-
- Assemble it correctly. Make sure your extruder is assembled correctly, according to the manufacturer’s instructions. If you bought a used or custom-made extruder, ask the person who sold it to you to cover the operation basics, if possible.
- Use moist clay that has been wedged well. This can’t be overstated. Just about any clay can be pushed through an extruder, but the results will vary enormously, depending on the characteristics of each. Clearly some clay bodies
are better suited to extruder work than others. As a general rule, any clay in a condition that is well suited for use on a potter’s wheel will work well in your extruder. This is not to say that you can’t use fresh clay right out of the bag.
But if it has been around awhile and it seems a little stiff, it will be more difficult to use in your extruder. You shouldn’t have to exert superhuman force to get the clay to move through the die. - Practice, practice, and more practice. Just about every tool or instrument requires some practice if you’re going to master it. If you’re new to extruding, give yourself and the extruder a chance.
- Working alone? Use the chest press method. Underfill the barrel so the handle is lower and closer to the barrel when you start. Now, standing directly in front of the extruder, square up your stance and press the handle with the center of your chest. This frees both of your hands to guide the clay as it extrudes.
- Cut off the first few inches. The first part of an extrusion never seems to come out straight. Cut it off squarely, then finish your extrusion. If you’re making a hollow extrusion, you can help it to come out straighter by pressing your flattened hand with slight upward pressure against the bottom of the extrusion as you pull on the handle with your other hand.
- Make a one-handed cut-off wire. Mount one end of a cutting wire or a piece of fishing line on the wall next to the bottom edge of the extruder. Let the other end hang free. After making an extrusion, support it from the bottom with one hand, then grasp the free end of your cutting wire and draw it through the clay along the bottom of your extruder.
- Center the die. If you want straight extrusions, the opening in the extruder die has to be centered in the barrel directly under the plunger. In a hollow-form die, the internal die pieces have to be centered relative to the perimeter walls of the die.
- Install dies off-center for curved extrusions. This won’t work with some extruders because their dies are fixed in one place, but if you can move yours from side to side or front to back, you might do some experimenting.
- Use a padded miter box. Use a padded miter box to make clean 90° cuts on the ends of your hollow extrusions. Wait until the extrusion has firmed up to a soft leather-hard, then lay it in the miter box. Use a cutting wire to cut through the clay using the notches as a guide. Line the bottom of your miter box with a piece of foam padding, which allows you to push your cutting wire all the way through the clay.
- Slice open a cylinder to make a slab. Cylinders made with an extruder can be cut down one side and laid flat to make a slab. If you have a cylinder die with a diameter of 3 inches, it will yield a slab approximately 9 inches wide. Recalling your high school geometry, the circumference of a circle equals the diameter times 3.14. To minimize warping, turn the slab over, curled edge down, before rolling it flat.
- Use paddles to help square up things. Square extrusions can be straightened by using two one-byfour-inch boards, each about a foot long. If the inside wall width is smaller than three inches, cut another board to fit inside the extrusion. With your extrusion resting on the table, slide the board inside and apply light downward pressure to flatten the extrusion wall. Hold one of the other boards in each hand and straighten the extrusion from the outside by squeezing the extrusion between the boards. Do this on all sides until the extrusion is square.
- True up cylinders from the inside out. Truing up cylindrical extrusions can be a little tougher. Look for a tube that fits snugly inside the extrusion after the clay has been allowed to firm up some. If necessary, wrap a tube with some paper to get the correct diameter and secure it with tape. Slide the tube into the extrusion with a twisting motion. If you’re making a vessel from the tube, do the straightening before adding the bottom. Otherwise air will get trapped, making it difficult to remove the tube.
- Save those inner tubes. If the clay leaks outside your screw- or twist-on type die holder, you can make a gasket that rests on the die from an old piece of car inner tube, or from gasket material you can buy at a car parts store.
- Keep your extruder clean! Unlike potter’s wheels, which seem to thrive on neglect, extruders need regular cleaning to do their job efficiently. The cleaning requirement can be one of the biggest turnoffs to extruder use, but it doesn’t have to be the drudgery some make it.
- Protect your dies and extend their lives. Spray a light, even coat of a silicone spray like WD-40, or a nonstick pan coating like Pam, over the parts that will be in contact with clay before loading the barrel. Use it sparingly each time you’re preparing to use your extruder.
- Remove clay before it dries. Do not let clay dry on the plunger plate or in the barrel. Dry clay is doubly hard to remove, and pushing the plunger through a barrel encrusted with dry clay can lead to excess wear on the plunger plate. Dried-on clay should be softened with a spray of plain water or a soap solution. It can then be scraped free with a rubber rib.
- Use cloth scraps to clean your barrel. Placing a piece of dampened denim cloth over the plunger and pushing it through the barrel helps clean the inside walls. If this doesn’t move well through the barrel, try a lighter weight material.
- Apply more leverage for small-opening dies. If your extruder comes equipped with a short handle and a longer handle, the longer handle will give you more leverage when trying to push clay through a die with a small opening. Having to resort to extra leverage may, however, indicate the need for moister clay. Clay that may seem too moist to handle at first may prove to be ideal when subjected to the extra compression of passing through a small die opening.
- Make a “gang” die to make coils more easily. Extruding a single, small-diameter coil can be very difficult if your extruder has a large barrel. Too much force is required to push the clay through the small opening. To make the job easier, use a four-place coil die, which is referred to as a “gang” die.
- Extrude some “test tubes.” Small-diameter, hollow tubes cut into short lengths make excellent pieces for testing glazes. Any of the common forms will work, but the hexagonal tube is especially useful. It can be set on end or laid on its side in the kiln to test glaze flow characteristics. Draw a pattern of lines down one side with a fork or a serrated rib. These will help you see how a glaze “breaks” over edges. Scratch code letters and numbers into the leather-hard test tube for identification. Hang these tubes on the wall or tie them to the handle of your glaze bucket with a piece of wire.
Â